Building efficient processes and tools frome prototyping to mass production.
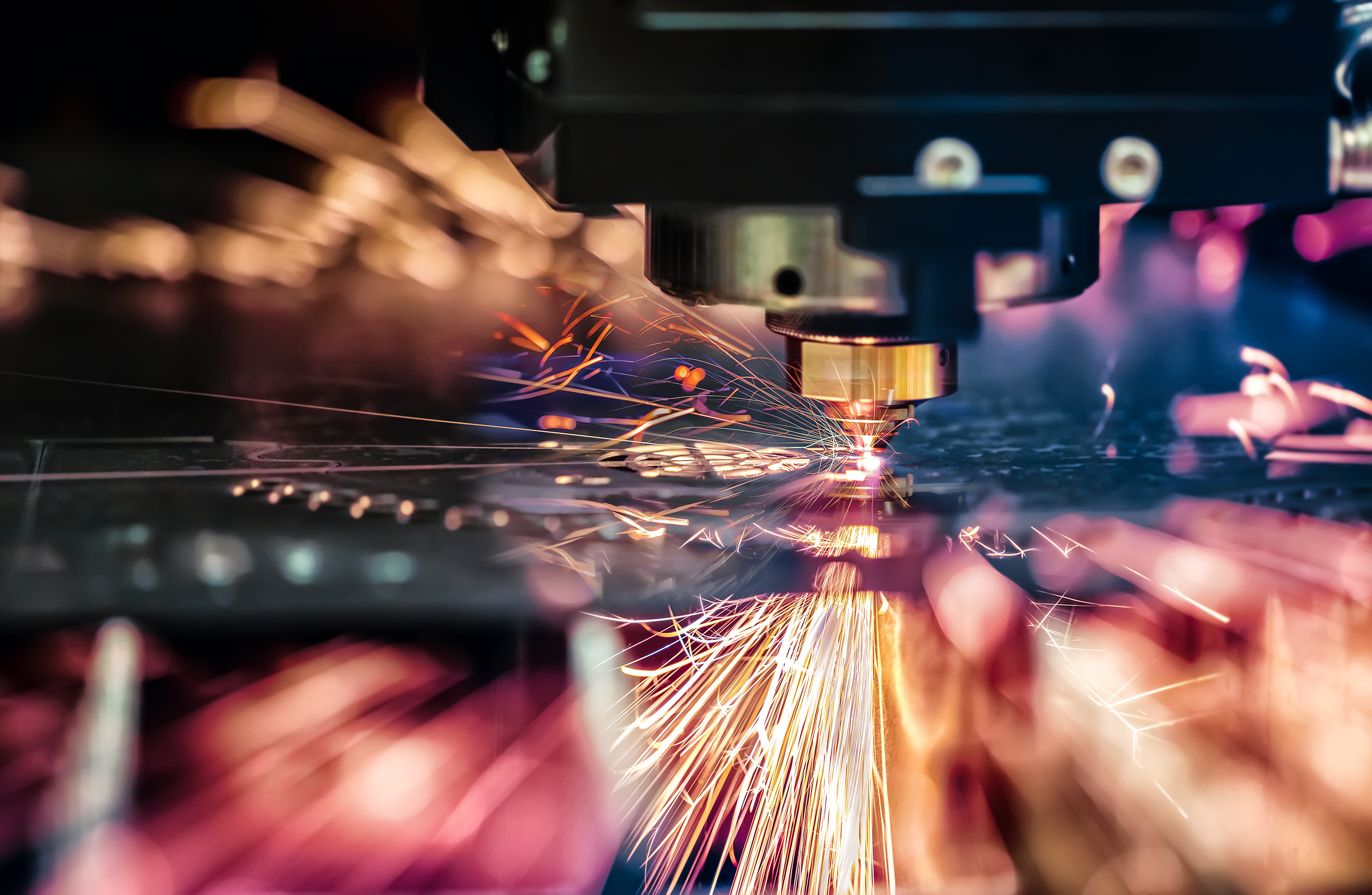
MasterSimon's Manufacturing Experience
The founder of MasterSimon Inc. Simon Duh and senior engineers have extensive manufacturing experience accumulated in Taiwan:1980_White Goods
1990_PC industry
2000_Consumer Electronics Industry
2010_ Experience with manufacturing processes up to this moment, precision mechanical components are perfectly assembled for each part regardless of appearance features or part tolerances.
Serious and responsible project management, cost management and risk management, production management .... On-time delivery to designated assembly plants or warehouses worldwide, please contact MasterSimon’s engineering team directly.

MasterSimon of Critical Components
& Sub Assembly
Is it too difficult to find an advanced technical supplier???
Yes, we do! MasterSimon provided 5-axis Milling and Mill-Turn.
Based on over 35 years of experience in precision machining and manufacturing processes, we will work closely with your team of mechanical engineers engaged in the development and production of Critical Components from prototyping to mass production.
We'll work with your engineering teams to build processes and tools to help the prototyping and engineering teams work more efficiently and actively unblock challenges that the team encounters.
The requests range from Critical Components to complete mechanical BOM management, including finishes and inspections for mass manufacturing.
Multiple technological areas are covered by the Prototyping and Engineering team's expertise. We will implement 5-axis Milling and Mill-Turn machining processes to achieve effective customer deliveries.

MasterSimon of Rapid Prototyping
Appearance Models
The advanced manufacturing technology behind your products
Based on the 35 years of product development experience accumulated by the founder of MasterSimon since 1984, he has led a team of professionals to serve numerous start-ups and large corporations, enabling the entire supply chain from development to mass production to be safely produced and manufactured in Taiwan. The founder and a group of experienced engineers review and analyze the appearance models.
3D printing cannot replace a team of experienced engineers
From 2010 to 2020, every country is developing, producing, and manufacturing 3D printing products. Of course, for non-precision size or special material verification, 3D printing is indeed a rapid prototyping option, but in terms of color, material, touch, and actual mass production weight, 3D printing cannot replace the review and analysis of appearance models by a team of experienced engineers with more than 35 years of experience.
From idea, design, and sketching...to mass production to bring the end customer's product to market successfully
Our team has rich experience in assisting our clients' designers from creativity, design, sketching...to mass production, and working with brands' design centers and design companies to achieve good teamwork to make products come true. To build a good relationship, we need not only good teamwork but also more empathy and originality, for the sake of the end customer how to smoothly bring the product to market is the biggest motivation.
The appearance model must present the greatest value in industrial design
From geometry and engineering drawings, we care about R-angles, C-angles, corners, arcs, ridges, and whether a plane is flat or not? Surface Treatment and Cosmetics of materials, how to present different surface variations, and color variations, this is the appearance model that must present the greatest value in industrial design.
"Creativity and design are made more beautiful by breakthroughs in process technology.
Products become brand marks because of rigorous process technology,
and cost control to win consumers' favor."
-MasterSimon-
Functional Models
Confidentiality
MasterSimon has maintained product confidentiality for more than 35 years before our products are ready for production. (Learn more: MasterSimon-SOLUTIONS)
MasterSimon OEM has developed a good habit of never disclosing end-user information and becoming a silent supplier. The highest level of professional ethics and confidentiality standards are established, maintained, and implemented within the factory and among our employees to maintain the security of our customers’ intellectual property.
- We sign and honor a Non-Disclosure Agreement with customers.
- Secure Rights Management Services system management for RFQ files.
- Data access restrictions through job assignment from IT systems to ensure that only project team members are authorized to access the project data.
- Employees are trained in product confidentiality and are required to sign a legally-binding product information security agreement.
- Product confidentiality training provided by legal counsel is arranged for all new employees at planned intervals.
- Stringent physical and environmental access controls are in place to ensure that only the responsible project team has access to the project workplace.
Mass production functional model, Product reliability, and On-time market launch
The strict process control and product confidentiality principle can be activated in Taiwan for the proprietary products of customers from Europe, America, Japan, Canada, Australia, and Israel. From BOM sheet to EVT prototyping and verification, NPI, DFM, cost analysis, yield analysis, and risk management are introduced in the process discussion of the functional model to ensure the assembly line goes online smoothly. Through a careful verification process that is close to the mass production functional model, product reliability and on-time market launch are the greatest values.
Perform critical product prototyping to mass production and turn start-ups from Start-Ups into core brand values
MasterSimon works hard to turn start-ups from Start-Ups into core brand values, and because MasterSimon exists to perform critical product prototyping to mass production, we strictly adhere to our OEM ethics of being a silent OEM and never revealing information about the end customer.
FAI First Article Inspection
- In the process of first production, the person in charge of the production line, inspectors should go to the production site to supervise and check the actual producer according to the production process, according to the current valid production process documents to complete the first piece, and to supervise and check each production process, problems found in a timely manner to correct and solve.
- The first production of regular production products and products produced by stopping and starting again must complete all production processes, and after the producer has passed the inspection and signed on the first piece card, then handed over to the inspector for first piece inspection. During the first piece inspection, the inspector should work with the person in charge of the production line to carry out the inspection according to the current valid drawings, lists, process documents and product requirements, and after passing the inspection, label the first piece of product and have it signed by the producer (or representative) and inspector on the first piece card. For the first piece of inspection due to larger changes to the product can be signed by the relevant personnel and inspection approval; first piece of inspection failed to immediately return, redo the first piece.
- The first batch production of new products and the semi-finished and finished products generated after the change of materials and specifications need to be inspected and confirmed.
- The first piece inspection should be done in time to make the first piece record and fill out the first piece confirmation.
- When quality problems are found in the production of the first piece, they should be reflected and handled in time, and the unqualified items should be reconfirmed. Only when the first piece is inspected and qualified, and the result is recorded on the first piece card, and the quality is approved by the inspector, can the production be organized.
- After the first part confirmation, the inspector can start the normal delivery inspection work.
Many special patented parts are available from EVT DVT PVT ..... Before preparing for mass production, both parties must establish a stable manufacturing process according to the engineering surface level specifications.
MasterSimon of CNC Machining
CNC Milling | CNC 5Axis Milling | CNC Turning |
CNC Turn & Mill | CNC Grinding | Wire Cut EDM |
Die Sinker EDM | Drilling EDM | Water Jet |
Laser Machine | Sheet Metal | Stamping |
Welding | Double Injection | Die Casting |

MasterSimon of Process Technology
Electrical Discharge, Wire Cutting, Heat Treatment, Subzero Treatment, Welding, Die Casting, Forging, Sheet Metal, Stamping, Plastic Molding, Die Casting, Double Injection, Laser Cutting, Laser Engraving, Water Jet, and PCBA.

MarterSimon of CMF LAB
We have a CMF lab where, beyond our ability to create or match any color, we can also create or match any material, gloss level, or surface treatments on demand. Upon completion, samples are shipped directly to our customer’s door for approval.
As part of the approval process, MasterSimon creates a gradient color sample for our customers with upper and lower limit ranges. This gives our customers a higher level of creative control before implementation on the mass production level.
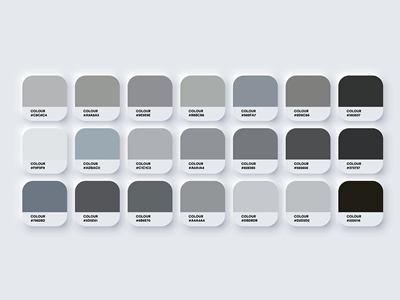
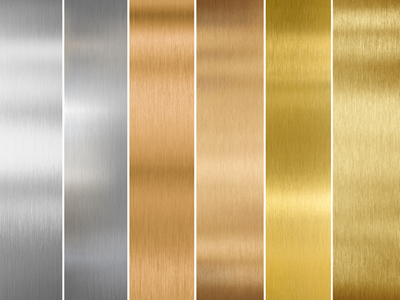
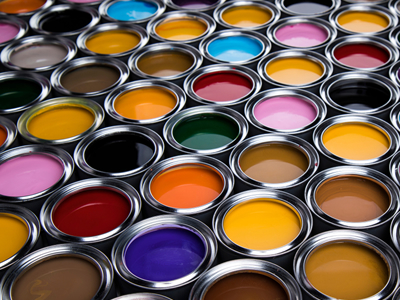
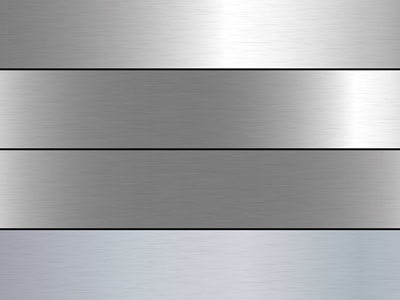

MarterSimon of Heat Treatment
Hardening, Sub-zero, Tempering, Solution, Aging, Annealing, Stress Relief.

MarterSimon of Heat Treatment Material
Stainless Steel, Tool Steel, Nickel Alloy, Copper Alloy, Titanium Alloy
- The aluminum License: 7075, 7050, 7475, 7055, 7155, 2024, 2124, 2014, 6061, 6082, 5083, 5052...etc.
- Stretched plate (stress relieved) with minimal deformation after processing
- Conforms to AMS-2154 compliant for aerospace materials
- Conforms toASTM flatness and thickness tolerances
- AMS heat treatment: T351, T651, T7351, T7751, T851, H321, H116, H131
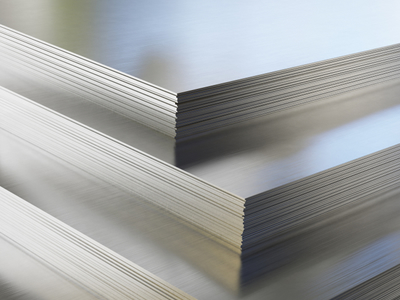
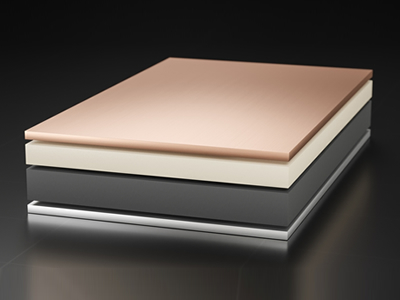

MarterSimon of Surface Treatment
- Plasma Chemical Coating-KEPLA-Coat
- Plasma Chemical Coating-MAGOXID-Coat
- Hard Anodizing
- Electroless Nickel Coating
- Electroless Nickel Coating with Dispersed PTFE
- Electropolishing
- Trivalent Chromium for Passivation
- Chrome-free Passivation of Mg-MAGPASS-COAT®
- Color Anodizing for Titanium
- Passivation for SST
- Black Oxide for SST
- Micro-Arc Oxidation
- Hard Anodizing for AL
- Black Film
- Electroless Nickel plating
- Electroless Nickel with Dispersed PTFE
- Electroless Nickel with Dispersed – Black
- Trivalent Chromium for Passivation
- Color Anodizing for TI
- Passivation for Stainless
- Black Oxide
- Sulfuric Acid Anodizing
- Sand Blasting
- Powder Coating
- Liquid coating
- Gilding
- PVD
- Salt Spray Test
- RoHS
To complete the task safely in polar and extreme climates.
Please contact MasterSimon’s engineering team directly.